Manufacturers, particularly those in the Food & Beverage industry, are in need of specific material-handling solutions that can be integrated into their automated production processes. When it comes to thermoformed plastics, an “off the shelf” solution is not always available. Customization is key to meeting the unique needs of an individual automation cell.
“A lot of injection molders offer standard containers, crates and pallets that they mass produce,” said Erik Larson, Allied Plastics Sales Manager. “A robotics company designing an automation cell for a manufacturer will sometimes find that those standard products will not work.”
Why?
To ensure that a plastic material-handling solution can function efficiently within an automated manufacturing process, the robotics provider is in need of extremely tight tolerances. Making the right material selection is the first step. For example, some material-handling solutions must exhibit a tight warping tolerance, and certain plastic materials provide for that. Additionally, a plastic product that is produced from a tooling machine, as opposed to the more typical casting process, can also hold tighter tolerances. The more options a plastics thermoformer has at its disposal, the more likely they’ll be able to come up with an effective solution.
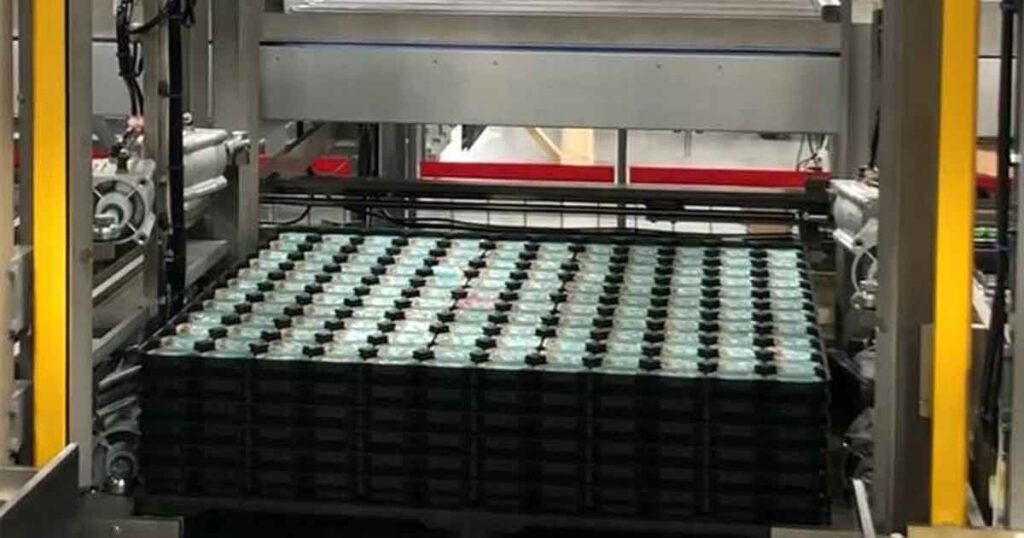
How Customization Can Come Into Play
Allied Plastics has been collaborating with manufacturers and robotics companies for many years to develop custom designs that meet an automation cell’s specific needs. Allied possesses the necessary expertise and tooling, along with a wide range of plastic material types, to create tailored solutions for a variety of products in a variety of industries.
“One of the first projects we did many years ago was a WIP (work in process) tray for a manufacturer of pinion and ring gears,” Larson pointed out.
The Food & Beverage industry is particularly well-suited to customization.
“When you think about the shear volume of product that Food & Beverage manufacturers are producing, it’s easy to see why automation has become so important,” Larson said. In many instances, an individual product has to be packaged and stored until it’s time to case-pack it for shipment to a retailer. Much of that product handling is automated, creating the need for a customized material-handling solution that will function reliably at different stages of the automated process.
Allied Plastics recently completed a project for a pet food manufacturer. The food product is placed into sealable packages before being placed into a plastic WIP tray manufactured by Allied. The tray advances down the production line to where it is picked up and placed in a stack. The entire process is automated.
“One of the challenges is that a robot cannot see things like a human can,” Larson explained. “The robot needs to be able to see where to pick the tray up. So we designed two white dots into the tray. That allows the robot to take a photo to orient itself, helping it know exactly what to do each time it goes to pick up another tray. Sometimes we design-in features like lifting plates or flat areas where a vacuum can suction the tray up. But in this case, adding two white dots was the most effective approach.
“We also needed to think about what we could do to prevent the robot from picking up more than one tray at a time,” Larson continued. “A human can see and feel if trays are sticking together. A robot cannot. So that required some additional design work.”
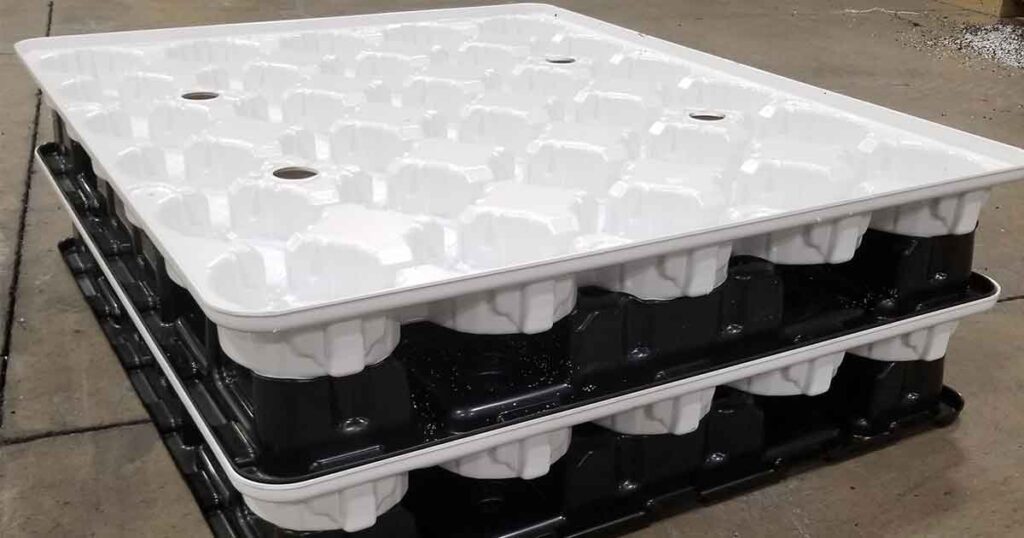
Working Together To Increase Productivity
While Allied Plastics has been developing custom solutions for automation cells for many years, Larson said interest is on the rise. That’s because manufacturing automation in general is on the rise.
“We develop custom solutions for many customers,” Larson said. “One of them started with a single automation cell several years ago. Now they have 70. Automation has allowed the company to grow over the years, without the need to eliminate employees. Robots have helped make the entire operation more productive.”
Allied Plastics is proud to have played a role in that kind of customer transformation. With any customer Allied works with, it always takes a collaborative effort to come up with the tailored solution needed for that particular automation application.
“The design process always starts with some good discussions between us, our end customer (the manufacturer) and the robotics company,” Larson said. “We need to understand the type of packaging or container that will be used. We need to understand how our product will ultimately work its way through the automation cell. We also need to know how our product will move in and out of the cell. We need to know the specific requirements at each of those stages so we can understand the tolerances we’re dealing with. That requires us, the manufacturer and the robotics company to all be on the same page from the beginning.” As part of that design process, it’s standard to start with a smaller lot size to run as a trial. This allows Allied Plastics to make any adjustments, if necessary, to get the final product dialed-in precisely. When developing material-handling solutions for manufacturing automation, precision is what it’s all about – and that requires customization from a plastics thermoformer with the capabilities to deliver.