Birdsong Peanuts is a peanut sheller headquartered in Suffolk, Virginia, that has shelling facilities in Virginia, Georgia and Texas.
Birdsong purchases its peanuts from local growers. The company then shells, cleans and sizes them before shipping to a long list of well-known consumer brands. “You’d be hard pressed to buy a peanut product in the grocery store and not touch Birdsong in some way, shape or form,” says J. Darden Langston Jr., Corporate Manager for Environmental Health and Safety at Birdsong Peanuts.
The majority of the peanuts Birdsong ships are placed into polypropylene tote bags. Each bag has a capacity of roughly 2,000 pounds and fits nicely on a standard 40×48 wooden pallet. But Birdsong Peanuts had been wrestling with a recurring problem for years. Those wooden pallets kept breaking and splintering. Little wooden fragments were finding their way into not only shipping containers, but sometimes the bags of peanuts themselves.
“When we switched to plastic pallets, we immediately saw a huge reduction in the amount of foreign material on the facility floors and making its way to our shipments and product,” Langston says.
Switching to plastic pallets wasn’t as easy as ordering out of a catalog, though.
Fast turnaround on a customized solution
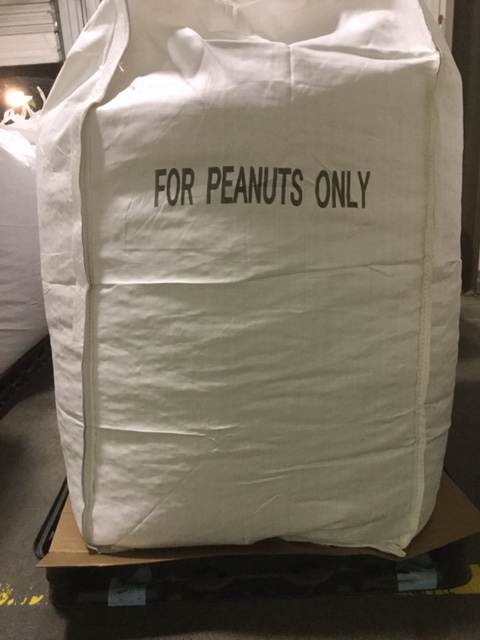
Prior to soliciting Allied Plastics’ help, Birdsong Peanuts looked at some standard plastic pallet options on the market. Most were built for storage racks which Birdsong did not have at its cold storage facilities. Plus, because those pallets were much heavier and more expensive than a wooden pallet, they simply didn’t make sense for what Birdsong was trying to accomplish. Birdsong Peanuts needed a customized solution.
Taking all of Birdsong Peanuts’ needs into account, Allied Plastics designed a structurally efficient, uniquely sized 44×44 plastic pallet that balanced strength, weight and cost.
Birdsong first came to Allied Plastics for help in August 2008. “By November, just a few months later, we were already making the production tool,” says Cory Buxengard, engineering manager at Allied Plastics.
Designing for unique storage needs
In Birdsong’s production operation, shelled peanuts are placed in large polypropylene tote bags. A single tote bag is placed on a pallet, and the pallet is sent off to a cold storage area. There the pallets are stacked four high to maximize space.
First and foremost, Birdsong’s new plastic pallets had to withstand the heavy loads that would be placed upon them. As mentioned earlier, each peanut-packed polypropylene tote bag weighs roughly 2,000 pounds. That meant the bottom pallet would need to support 8,000 to 9,000 pounds.
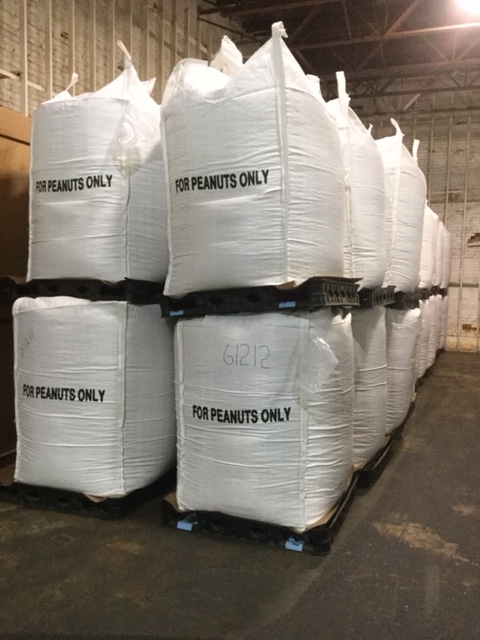
“Because Birdsong wanted to stack these totes in multiple layers, we knew our normal pallet design would not work,” Buxengard says. “Our typical pallets have nine legs, so we would essentially be balancing each layer on top of a center leg. Structural foam pallets contain a framework that ties all of the legs together, but they end up flexing and breaking too much. It’s also difficult for a forklift operator to insert the forks to lift those foam pallets up. So we knew that any plastic pallet we designed would need to be capable of taking the same load on both the top and bottom. We also had to address that compression issue so a forklift could easily remove each pallet layer.”
Buxengard says the final design allows for a pallet to be picked up from either the front or back — but both sides are closed off. “That design allows us to carry a lot of structure from the front to the back to help distribute the weight load,” Buxengard explains.
As durable as these new plastic pallets needed to be, they also needed to be fairly light.
“Sometimes our pallets need to be handled by hand on the production line,” Langston says. “A pallet weighs 42.5 pounds so it isn’t too difficult. I remember going through several stages of testing and refining, trying out different plastic thicknesses. Eventually we settled on a thickness we felt was the most appropriate in terms of strength, balance and cost.”
To help determine the optimum plastic thickness, Birdsong Peanuts and Allied Plastics came up with a clever process. Three thicknesses were tested. For each, a unique color was incorporated into the tube runners where the forklift forks are inserted. This way, Langston’s team could quickly identify which thicknesses were holding up and which weren’t.
Designing for unique shipping needs
When product is removed from cold storage and shipped to a customer, Birdsong Peanuts never ships the pallets. Rather, a corrugated slip sheet is placed between the pallet and the bottom of the tote bag. This allows the slip sheet and tote bag to be removed by a forklift and placed in a shipping container. The pallets, then, are returned to Birdsong’s production line.
After those first couple years of testing different material thicknesses, Langston says the customized pallets from Allied Plastics haven’t changed much — because they haven’t had to.
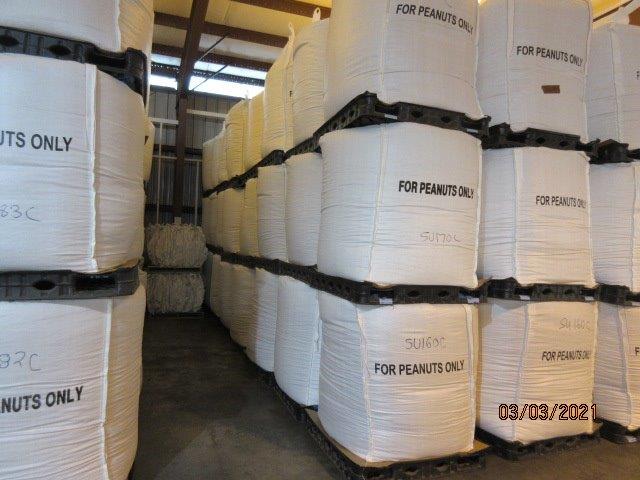
One mild design update was born out of the need to make the slip sheets easier to work with. “We added some channels onto the deck of the pallet so a forklift driver could insert the forks under the slip sheet and easily move the totes onto a trailer or other shipping container,” Buxengard says.
Since Birdsong Peanuts switched to the customized plastic pallets around 2009, the company has continued to place orders annually. Langston says he and the entire Birdsong management team have been astonished by how well the pallets continue to hold up.
“We wouldn’t go three cycles on our old wooden pallets before they started breaking apart,” Langston recalls. “I can’t even tell you how many cycles these plastic pallets can go, because it’s too many to count. They last years and years, to say the least. None of us really knew what to expect. But I can honestly say that these plastic pallets have been one of the most profitable capital improvement investments we’ve ever made.”
For more information, or to discuss a problem you are having, Contact Us Today.