Allied Plastics offers a concentrated line of standard industrial packaging options. However, most of the packaging products the company thermoforms are customized to a given customer’s particular needs.
“The majority of our packaging customers come to us for a solution they can’t readily buy off of the shelf,” says Erik Larson, packaging sales manager at Allied Plastics. “Then our engineering and sales teams work together with the customer to come up with the right solution.”
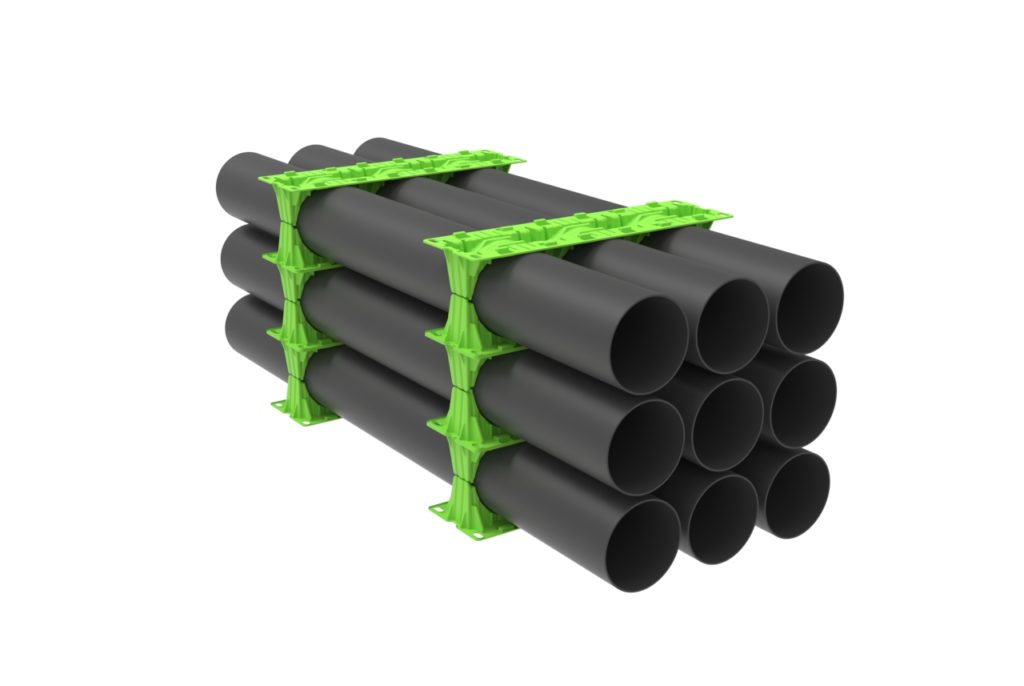
In this case, the right solution was a high-density polyethylene (HDPE) roll cradle that would provide a safer and more efficient way to stack and ship liner pipes. The customer was experiencing numerous frustrations with its existing method of shipping. The large, cylindrical pipes were simply being stacked and banded together on huge wooden pallets.
“First and foremost, the customer had concerns from a safety standpoint,” Larson says. It was difficult for the customer’s employees to pull product off of a trailer because the product was not stable on the pallet. Additionally, as a result of being stacked directly on top of one another, some of the product became deformed while in transit. Some product even ended up rolling off of the pallet, oftentimes leading to damage so significant that it had to be scrapped.
“After doing some online research, the company found us and gave us a call,” Larson says. Roll cradles have long been used to store and transport all kinds of cylindrically shaped products. But most are made of wood and prone to breaking. The customer wondered if a customized roll cradle could be thermoformed. Larson told them it could, and that the durability and longevity of a plastic roll cradle would be unmatched.Solving four problems at once
After discussing the project with the customer, Allied Plastics began developing a solution that would solve the customer’s four primary objectives:
- Improve safety
- Help maintain product integrity during shipping
- Reduce amount of material handling
- Reduce frequency of empty packaging shipments back to supplier
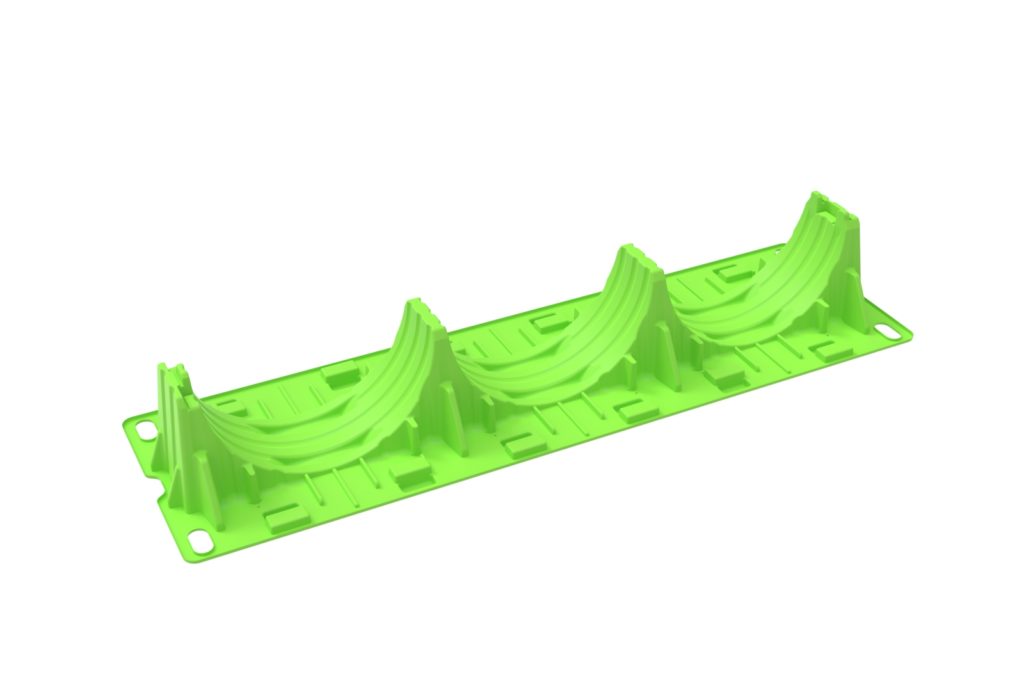
To begin addressing the first two objectives, strong HDPE roll cradles were designed specifically for the 27-inch-diameter liner pipes. The cradles would stabilize the pipes during transit while also helping to maintain their shape. The cradles were designed so they could be inverted, allowing both the cradle and the pipe to support the weight above it. The cradles were also designed to interlock for increased stability from one layer to the next. Finally, a banding channel was designed into the cradle so an entire stack of liner pipes could be strapped down during shipping.
Based on the customer’s customized needs, this solution allows nine liner pipes to be shipped in a stack (three layers of three). Due to the length of the pipes (20 to 40 feet), three roll cradles are used per layer to optimize stability and support the weight.
Cradle durability was also a focus. Allied Plastics’ engineers chose a material thickness that matched up well to the size and weight of the product being shipped.
“With a typical wooden cradle or pallet, we’ve heard from customers that they might get five trips before it starts to break,” Larson says. “With our plastic roll cradles, unless one is damaged by a forklift or mishandled, you’ll easily get over 100 trips.”
To further meet its efficiency objectives, the customer switched from a wooden pallet with casters to metal carts to serve as the base of the stack. The metal carts are smaller and lighter, yet more durable. Like with the roll cradles, three metal carts are used per stack to optimize stability.
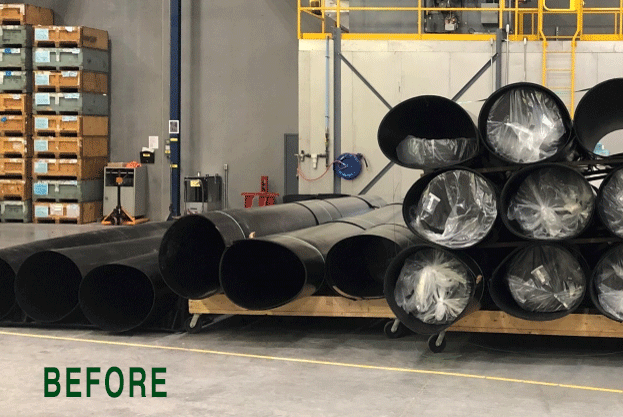
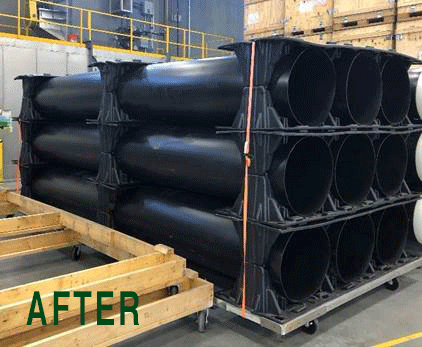
The thermoformed roll cradles help provide another efficiency improvement. The customer needs to put its liner pipes through an annealing process before placing them into service. When a shipment comes in, a stack of nine pipes is held securely in place by the plastic roll cradles, making it easy for an employee to wheel the stack off of the trailer. And because the roll cradle is made from a PE material similar to the liner pipe, that entire stack can be rolled directly off of the trailer and into an annealing oven, eliminating the inefficiency of having to double-handle the pipes. The current process was to unload the pipe into a separate cart and then transfer them into the annealing oven.
Finally, there is one more efficiency gain. Both the metal carts and plastic roll cradles are designed to nest together snugly when empty, allowing roughly four times as many units to be shipped back to the supplier than the previous wooden carts. At a time when transportation costs are on the rise, being able to significantly reduce the number of return trips to the supplier adds up quickly.
Allied Plastics understands what it takes to make a durable, versatile custom packaging solution that helps meet its customers’ unique customized needs. Need a better packaging solution for your product? CONTACT US TODAY!