Unlike other materials such as aluminum or fiberglass, thermoformed plastic parts do not need to be painted. That helps save time and money while delivering a finished product of superior durability and appearance.
Wait a second … how can an unpainted part have superior durability and appearance? Great question, but don’t worry. Just because the plastic part doesn’t go through a traditional painting process doesn’t mean it ends up looking bland and ugly.
When a plastic part is thermoformed, the color is molded right into the plastic sheet that goes through the thermoforming process. And you’re not limited to a handful of traditional colors, either. In fact, there are literally thousands of color possibilities.
There are other benefits to having the color molded-in during the thermoforming process:
- Looks great right out of the mold with no curing time necessary
- Crisper depth of image
- No orange peel
- Excellent UV protection
- No spraying, fumes or material waste
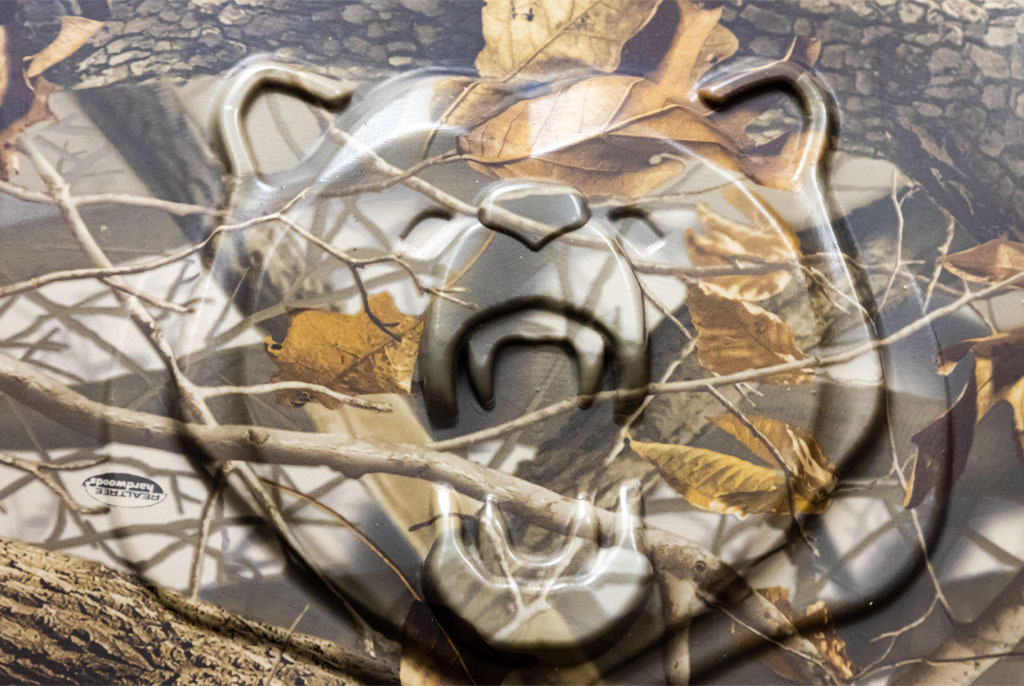
So how does it work?
Allied Plastics addresses color selection during the early stages of project planning with the client. Sometimes Allied Plastics helps come up with the perfect color choice. Other times, the client already has a color in mind.
Once a color has been selected, Allied Plastics reaches out to its color compounder. Step one is matching the color.
“We’ll typically give our compounder a pantone number or RAL Color Chart number,” says Jon Larson, OEM Sales Manager at Allied Plastics. “When the client already has a color in mind, they’ll often provide us with an existing part or color chip which we then pass along to our color compounder. Whatever the case, the color matching process is pretty straightforward and only takes a couple of weeks.”
From there the color compounder does its thing, ultimately shipping the colored resins to Allied Plastics. Allied then heats those resins up, melts them down, and integrates them into the plastics sheets to be utilized in the thermoforming process.
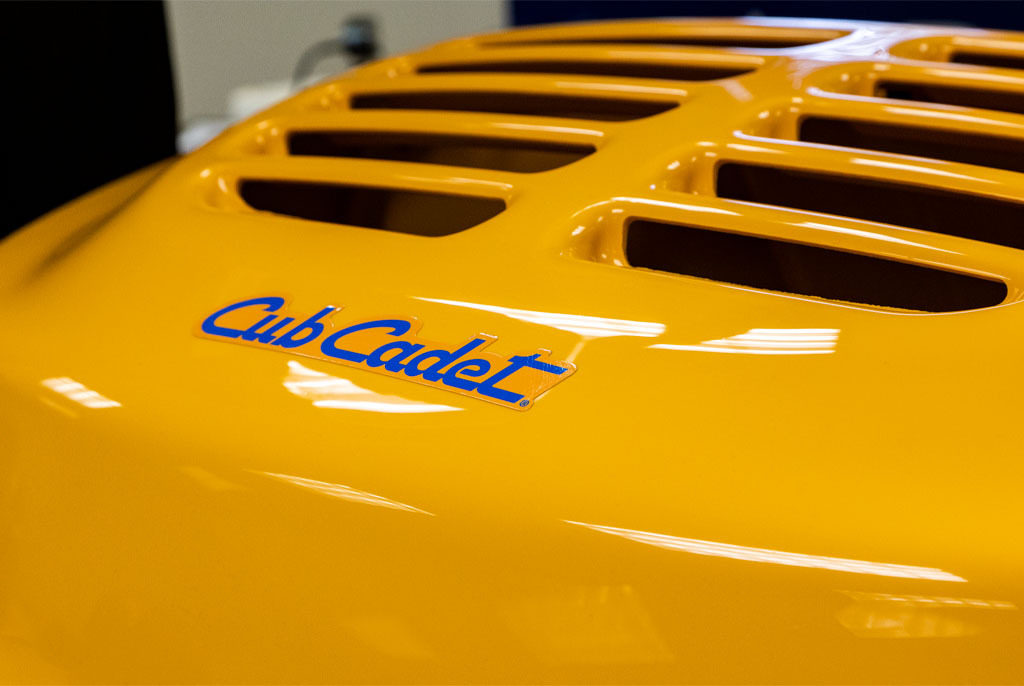
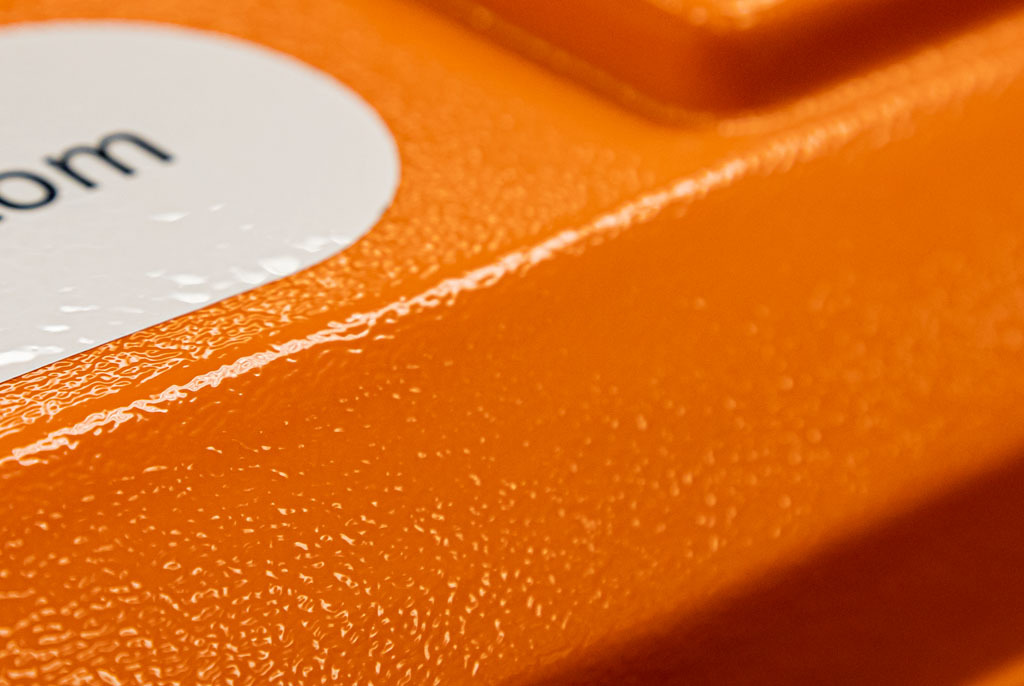
Allied Plastics is uniquely proficient at this because it has been operating its own in-house extrusion line since 2017. During the extrusion process, plastic pellets are mixed, melted and conveyed into a dye that turns the plastic into a sheet profile. Incorporating color into that process is seamless.
Another unique in-house capability is producing custom laminated films. This allows clients to get even more creative with the finished look of their products. Laminated films provide a durable finish in eye-catching treatments such as metallics, brushed metal, wood grain and carbon fiber. Laminated films can be applied during the extrusion process or after the sheets have been formed. Either way, it’s common to apply those films over a black or neutral-colored substrate. But again, no painting is necessary to deliver a durable, attractive product.
Of course, there are some occasions when a plastic part must undergo a traditional painting process, such as when the quantity is very small or the part requires multiple colors. “With 95% of the plastic parts we produce, however, no painting is necessary,” Larson points out. “For the other 5%, we’ve partnered with a specialized paint shop that can efficiently deliver the quality we expect.”
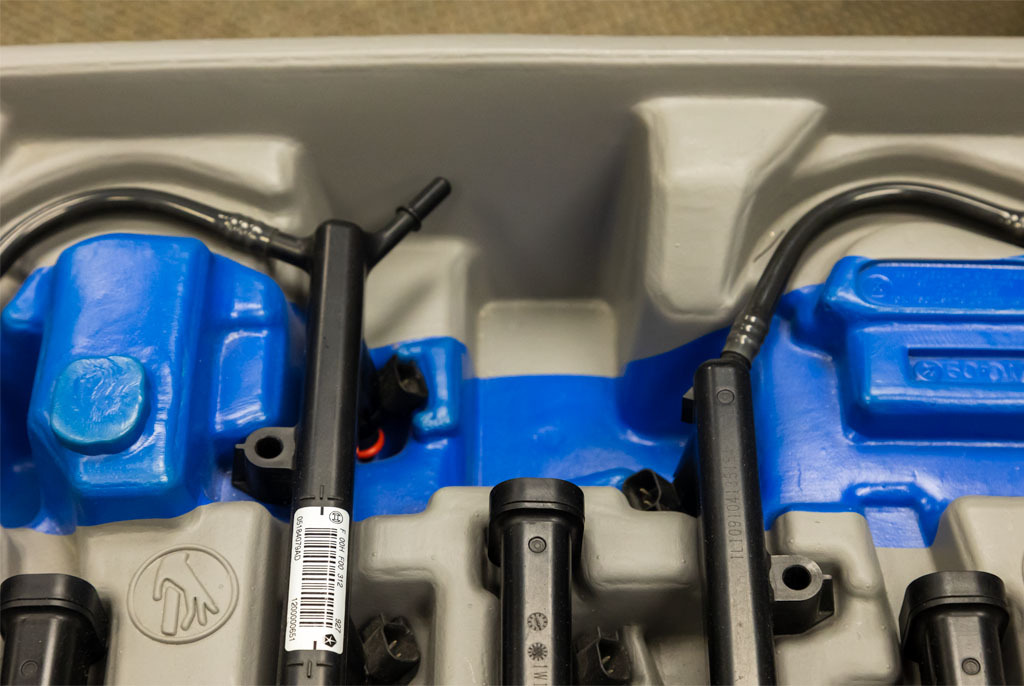
Those instances are pretty few and far between, at least at Allied Plastics. That’s because Allied can handle sheet extrusion, color integration, and film lamination all in-house — helping clients save time and money while getting a superior finished product that looks great and will last.